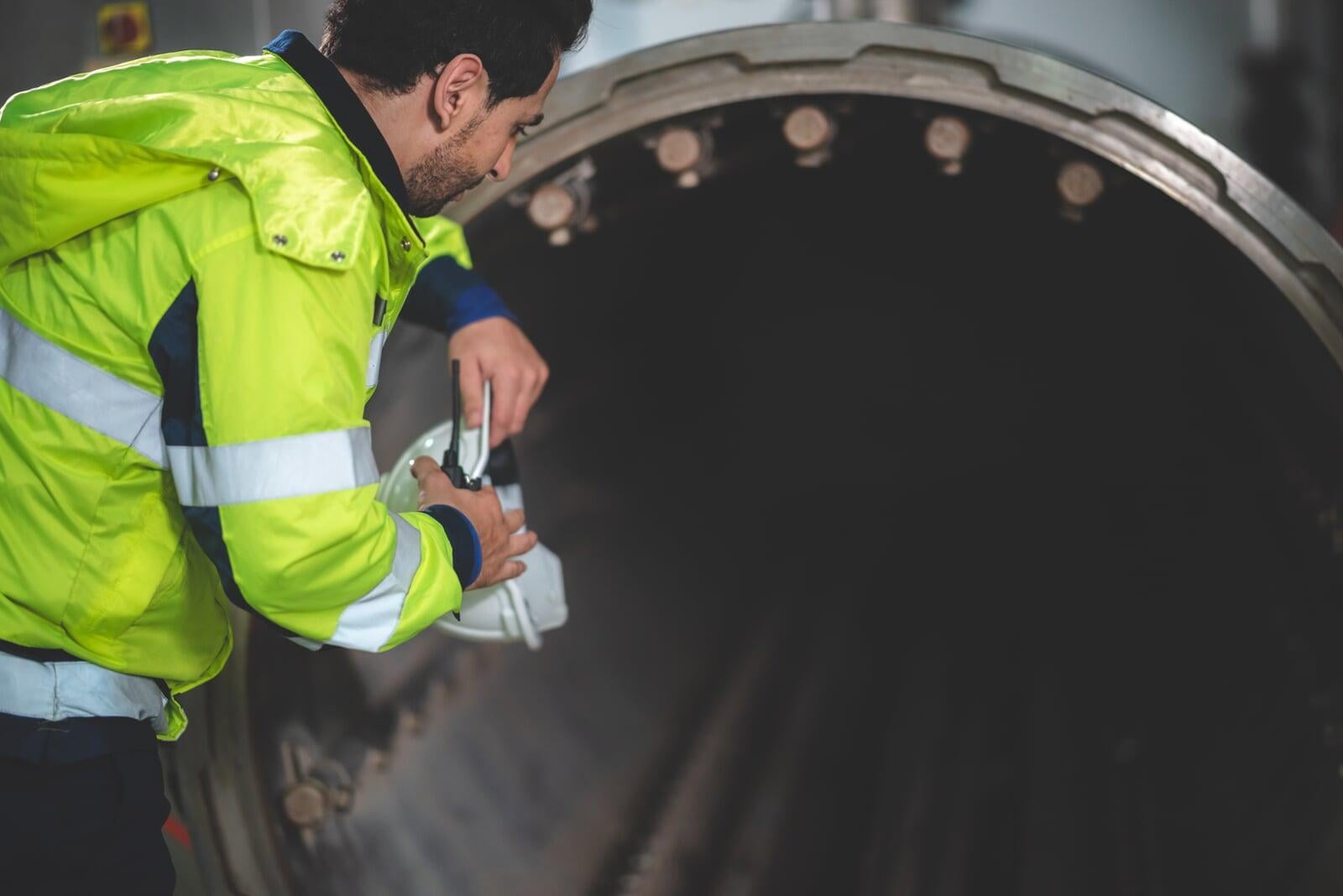
Anomaly Detection
IECM can be used to detect anomalies in corrosion monitoring data and alert operators to potential problems.
Underground pipelines are a critical component of many industries, including oil and gas, water supply, and wastewater management. These pipelines are subject to corrosion, which can lead to leaks, failures, and safety risks. To prevent these issues, it is essential to have a robust corrosion monitoring system in place. However, detecting anomalies in corrosion monitoring data can be challenging, and operators need to have the right tools and knowledge to identify potential problems. In this article, we will discuss best practices in underground pipelines that can be used to detect anomalies in corrosion monitoring data and alert operators to potential problems.
The first best practice is to have a comprehensive corrosion monitoring system in place. This system should include a range of sensors, including ultrasonic sensors, electrochemical sensors, and magnetic flux leakage sensors. These sensors should be placed at strategic locations along the pipeline to monitor its condition continually. The data collected by these sensors should be transmitted in real-time to a central monitoring system, where it can be analyzed using specialized software programs.
The second best practice is to establish a baseline for the pipeline's condition. By collecting data on the pipeline's condition over time, operators can establish a baseline for its normal operating condition. Any deviation from this baseline can be an indication of potential problems, allowing operators to take action before the issue becomes significant. Mechanistic models quantify the severity of the deviations from normal operation because they respond immediately in a change in IR-free or corrosion rate without the need of historical data (similar events that occurred in the past). Even what-if scenarios could be run for computing the impact of planned or unplanned changes in the operational conditions.
The third best practice is to use advanced analytics to analyze the data collected by the corrosion monitoring system. Machine learning algorithms can analyze large datasets to identify patterns that may be associated with corrosion, allowing operators to predict when maintenance is needed. Additionally, these algorithms can identify anomalies in the data that may indicate potential problems, alerting operators to take action.
The fourth best practice is to have a comprehensive inspection and maintenance program in place. Regular inspections and maintenance are essential for identifying potential problems before they become significant issues. By conducting regular inspections and maintenance, operators can identify areas that require repair or replacement, reducing the risk of leaks or failures.
The fifth best practice is to train operators and personnel to understand the data collected by the corrosion monitoring system. Operators and personnel should be familiar with the data collection process, the types of sensors used, and how to interpret the data. This knowledge can help operators to identify potential problems and take action before the issue becomes significant.
In conclusion, best practices in underground pipelines can help operators to detect anomalies in corrosion monitoring data and alert them to potential problems. By having a comprehensive corrosion monitoring system in place, establishing a baseline for the pipeline's condition, using advanced analytics to analyze the data, having a comprehensive inspection and maintenance program in place, and training operators and personnel to understand the data, operators can reduce the risk of leaks, failures, and safety risks. As technology continues to advance, it is likely that best practices will become even more effective, allowing for safer and more reliable underground pipelines in the future.